Home / Chemicals & Materials / Advanced Materials / 3D Printing Metals Market
3D Printing Metals Market Size, Share & Industry Analysis, By Technology (Power Bed Fusion, Binder Jetting, Direct Energy Deposition, and Others), By Metal (Aluminum, Stainless Steel, Titanium, Nickel, and Others), By Application (Aerospace and Defense, Automotive, Healthcare, and Others), and Regional Forecast, 2024-2032
Report Format: PDF | Latest Update: Feb, 2025 | Published Date: Dec, 2024 | Report ID: FBI110817 | Status : PublishedThe global 3D printing metals market size was valued at USD 2,013.9 million in 2023. The market is projected to grow from USD 2,478.5 million in 2024 to USD 10,893.1 million by 2032 at a CAGR of 20.3% during the forecast period. North America dominated the 3D printing metals market with a market share of 41.17% in 2023.
3D printing metals, also known as metals additive manufacturing, is a process that creates three-dimensional metal objects by layering Metals powder or wire and fusing them with heat sources, such as lasers or electron beams. This technology allows for complex geometries and customized parts that are difficult to produce with traditional manufacturing methods. Its ability to reduce waste, decrease production time, and create lightweight yet strong components is driving the market growth. Industries such as aerospace, automotive, and healthcare are adopting this technology to innovate designs, improve performance, and potentially lower costs in the long run.
The COVID-19 pandemic initially disrupted the 3D printing metals market, causing supply chain issues and reduced demand in sectors such as aerospace. However, it also spurred innovation, with 3D printing metals being used to produce medical equipment and component for ventilators rapidly. As economies recovered, the market saw renewed growth. Increased focus on supply chain resilience and localized manufacturing boosted the adoption of 3D printing metals technologies.
3D Printing Metals Market Trends
Expansion of 3D Printing Metals Market Driven by Personalized Implants, Advanced Surgical Tools, and Biomedical Innovation in Healthcare
The healthcare industry is creating huge prospects for the 3D printing metals market through a variety of critical applications. Personalized implants are at the forefront of this growth, as 3D printing enables the manufacture of custom-fit implants based on specific patient anatomy. This customization leads to better outcomes in orthopedic, cranial, and dental operations. Similarly, the technology permits the development of lightweight, long-lasting, and precisely fitting prosthetic limbs and orthotic devices, improving patient comfort and function.
3D printing metals is transforming the surgical tool industry by enabling the swift development of customized or specialized surgical instruments. This improves surgical precision and efficiency, which could lead to better patient outcomes. The method also speeds up medical device prototyping, lowering time-to-market for innovations. In biomedical research, 3D printing enables the development of complex structures for tissue engineering and drug delivery systems, pushing the limits of medical science’s capabilities.
Dental applications are another significant area of opportunity, as 3D printing allows for the precise manufacture of crowns, bridges, and other dental prosthetics. In orthopedics, the technology enables the development of spine and joint implants with porous architectures that promote metals is being utilized to build patient-specific anatomical models, which can help with surgery planning and medical education.
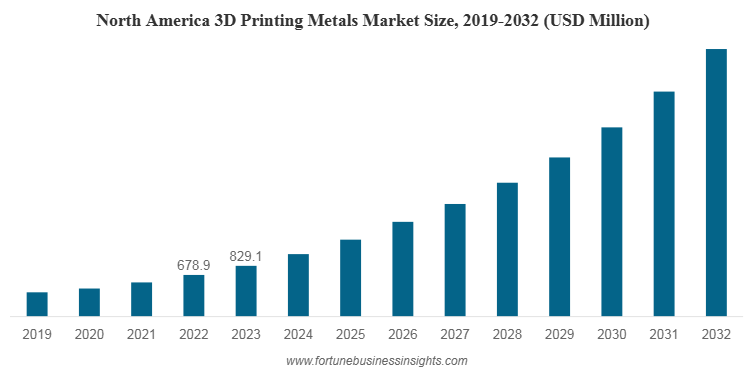
3D Printing Metals Market Growth Factors
Lightweight Components, Rapid Prototyping, and On-Demand Production in Aerospace & Defense Industry to Bolster Market Growth
The aerospace and defense industry is a major driver of the 3D printing metals market, driving innovation and embrace across a variety of applications. This technology’s capacity to build complex, lightweight components is especially significant in this sector since it reduces aircraft weight while enhancing fuel efficiency and performance in both commercial and defense applications. Rapid prototyping enables faster design iterations and testing of new components, resulting in shorter product development cycles and lower costs.
Additionally, 3D printing facilitates parts consolidation, where complex assemblies can be redesigned as single-printed parts, simplifying supply chains and reducing the number of components. The sector also benefits from on-demand spare parts production, which reduces inventory costs and aircraft downtime. Custom tooling, advanced propulsion system components, and specialized satellite parts are other areas where 3D printing is making significant impacts.
In the defense sector, the technology is employed to manufacture specialized equipment, vehicle components, and even ammunition, resulting in tactical advantages and cost savings. The aerospace and military sector’s stringent requirements for high-performance, lightweight materials, and complicated geometries make it an excellent candidate for 3D printing metals technologies, which are driving market growth and technological breakthroughs throughout the industry.
RESTRAINING FACTORS
High Costs, Limited Materials, and Quality Control Challenges Restrict Growth of 3D Printing Metals Market
The 3D printing metals market growth faces several significant restrictions despite its potential and increasing adoption. High initial investment costs for equipment and materials remain a major barrier, particularly for small and medium-sized enterprises. This financial hurdle is compounded by the need for specialized training and expertise to operate complex 3D printing systems effectively. Additionally, the limited range of metals materials suitable for 3D printing compared to traditional manufacturing methods restricts the technology’s applicability in certain industries.
Quality controls and consistency issues also pose challenges, as 3D-printed metals parts may exhibit variability in mechanical properties or require extensive post-processing. This can lead to concerns about reliability, especially in critical applications. Furthermore, the relatively slow production speed of metals 3D printing compared to traditional mass production techniques limits its use in high-volume manufacturing scenarios. Regulatory uncertainties in some industries, particularly aerospace and medical, can also hinder widespread adoption, as certification processes for 3D-printed parts are still evolving.
3D Printing Metals Market Segmentation Analysis
By Technology Analysis
Power Bed Fusion Dominated Market Owing to Increasing Use in Automotive Industry
Based on technology, the market is classified into power bed fusion, binder jetting, direct energy deposition, and others.
The power bed fusion segment held the highest share of the global market in 2023 and is estimated to record a significant growth rate during the forecast period. Powder bed fusion offers high precision and is widely used in the automotive industry. The growth in this segment is driven by increasing demand for complex geometries in high-value industries, continuous improvements in process speed and build volume, and the growing adoption of mass customization applications.
Binder jetting is gaining traction due to its faster build speeds and lower costs compared to PBF technologies. It is particularly suitable for larger parts and higher volume production. The growth factors for binder jetting include rising interest in high-volume metals parts production, lower equipment and operational costs, and advancements in binder and sintering technologies.
By Metal Analysis
Titanium Dominated Owing High Strength To Weight Ratio, Making It Valuable In Aerospace Industries
Based on metal, the market is classified into aluminum, stainless steel, titanium, nickel, and others.
The titanium segment held the highest share of the global market in 2023. Titanium has a high strength-to-weight ratio, making it valuable in the aerospace industry, where reducing weight while maintaining structural integrity is crucial. The biocompatibility of titanium has led to its widespread adoption in the medical field, particularly for implants and prosthetics. The ability to create complex, customized titanium parts through 3D printing has revolutionized industries such as healthcare and aerospace, contributing to significant titanium demand.
Aluminium has gained significant traction in the 3D printing market due to its lightweight properties and corrosion resistance. This metals is particularly favored in industries such as aerospace, automotive, and consumer goods manufacturing. This relatively low cost of aluminum powder compared to other metals powders has contributed to its growing adoption in additive manufacturing processes.
By Application Analysis
Aerospace and Defense Dominated Market Due to Technological Advancements and Innovations
In terms of application, the market is segmented into aerospace and defense, automotive, healthcare, and others.
The aerospace and defense segment held the largest 3D printing metals market share in 2023. This industry utilizes additive manufacturing for producing complex lightweight components, prototypes, and spare parts. The ability to create intricate geometries and reduce part weights is particularly valuable in aircraft and spacecraft design. Growth factors include increasing demand for fuel-efficient aircraft, the need for rapid prototyping and testing, and the potential for on-demand spare parts production in remote locations.
The automotive industry is leveraging 3D printing metals for prototyping, tooling, and the production of specialized components. This technology enables faster design iterations, weight reduction in vehicles, and the creation of complex parts that enhance performance. Growth in this segment is driven by the push for electric and hybrid vehicles, the need for lighter and more fuel-efficient cars, and the trend toward mass customization in the automotive market.
REGIONAL INSIGHTS
By region, the market is segmented into North America, Europe, Asia Pacific, Latin America, and the Middle East & Africa.
North America occupied the dominant part in the market share and was valued at USD 829.1 million in 2023. The region’s dominance is driven by substantial investment in research and development, a strong presence of key market players, and early adoption of advanced manufacturing technologies. The region’s robust automotive and defense sectors also contribute to market growth. Key factors include government initiatives supporting additive manufacturing and a well-established industrial base.
The Asia Pacific region is experiencing the fastest growth in the market. China, Japan, and South Korea are leading this growth with rapid industrialization and increasing adoption of advanced manufacturing technologies. The region’s expanding aerospace, automotive, and healthcare sectors are major contributors to market expansion. The availability of raw materials and lower production costs also make this region attractive for market development.
Europe represents another major market. Countries such as Germany, the U.K., and France are at the forefront of adopting metals 3D printing technologies. The region’s strong aerospace and automotive industries are primary drivers of market growth. European companies have been particularly innovative in developing new metals powders and 3D printing technologies. The region also benefits from supportive government policies promoting Industry 4.0 initiatives and sustainable manufacturing practices.
In Latin America, countries such as Brazil and Mexico are seeing increased adoption in their automotive and aerospace industries. The region’s growing manufacturing sector and increasing awareness of the benefits of additive manufacturing are driving the market expansion.
The Middle East & Africa region is an emerging market. Countries in the GCC, particularly the UAE and Saudi Arabia, are investing in additive manufacturing technologies as part of their economic diversification strategies. The region’s oil and gas industry is exploring metals 3D printing for producing spare parts and reducing inventory costs. In Africa, South Africa leads in adoption, particularly in the automotive and aerospace sectors. While the market is still developing, there’s growing interest in using metals 3D printing for healthcare applications across the region.
KEY INDUSTRY PLAYERS
Key Players to Adopt Organic and Inorganic Business Growth Strategies to Maintain Dominance in Market
Key market players in the market are focusing on expanding product portfolios through R&D, investing in advanced manufacturing facilities, and forming strategic partnerships. They’re also acquiring innovative companies, developing industry-specific solutions, and improving software integration. Sustainability efforts include metals powder recycling programs. Companies are offering training and support services to facilitate technology adoption. These initiatives aim to strengthen market positions, drive innovation, and cater to growing demand across various industries, particularly aerospace, healthcare, and automotive sectors.
LIST OF TOP 3D PRINTING METALS COMPANIES:
- EOS GmbH (Germany)
- SLM Solutions (Germany)
- Desktop Metal, Inc. (U.S.)
- GE Additive (U.S.)
- 3D Systems, Inc. (U.S.)
- Xi'an Bright Laser Technologies Co., Ltd. (BLT) (China)
- Stratasys (U.S.)
- Velo3D, Inc. (U.S.)
- TRUMPF (U.S.)
- Shanghai Hanbang United 3D Tech Co., Ltd. (China)
KEY INDUSTRY DEVELOPMENTS:
- April 2024: EOS introduced the EOS Aluminium AlSi10Mg in the Responsible Products portfolio. The company is committed to reducing the climate impact of manufacturing. EOS Aluminium AlSi10Mg is a minimum of 30% recycled feedstock.
- February 2024: EOS announced the commercial availability and successful development of new EOS CopperAlloy CuNi30 material. The material delivers superior performance and material properties with a combination of ductility and high strength.
- November 2023: Nikon SLM Solutions and Materialise partner to develop and build processors for Nikon’s 3D printers, integrating them into Materialise’s CO-AM platform. This collaboration aims to enhance metals additive manufacturing, offering manufacturers customization options.
- October 2023: EOS announced the addition of new EOS Aluminum Al5X1. It is an aluminum alloy specifically engineered for Additive Manufacturing (AM) at a competitive cost compared to other aluminum alloys with similar elongation and strength properties.
- July 2022: EOS introduced four new metals materials for additive manufacturing for the EOS M 290 metal system, which includes one tool steel, two stainless steel, and one nickel alloy. These materials are employed in extreme conditions, difficult environments, and in elevated temperatures.
REPORT COVERAGE
The report provides a detailed analysis of the market. It focuses on key aspects, such as leading companies, metals, technology, and the application of the product. Besides this, it offers insights into the market and current industry trends and highlights key industry developments. In addition to the factors mentioned above, it encompasses several factors contributing to the market's growth.
Report Scope & Segmentation
ATTRIBUTE |
DETAILS |
Study Period |
2019-2032 |
Base Year |
2023 |
Estimated Year |
2024 |
Forecast Period |
2024-2032 |
Historical Period |
2019-2022 |
Unit |
Value (USD Million) and Volume (Kiloton) |
Growth Rate |
CAGR of 20.3% from 2024 to 2032 |
Segmentation |
By Technology
|
By Metal
|
|
By Application
|
|
By Region
|
Frequently Asked Questions
How much is the 3D printing metals market worth?
Fortune Business Insights says that the global market size was valued at USD 2,013.9 million in 2023 and is projected to record a valuation of USD 10,893.1 million by 2032.
What was the value of the North America 3D printing metals market in 2023?
In 2023, the North America market value stood at USD 829.1 million.
At what CAGR is the market projected to grow during the forecast period of 2024-2032?
Recording a CAGR of 20.3%, the market will exhibit steady growth during the forecast period.
What was the leading segment in the market by application?
In 2023, the aerospace & defense application was the leading segment in the market.
What is the key factor driving the market?
Growing demand from the automotive industry will drive the growth of the market.
Which region held the highest market share in 2023?
Asia Pacific held the highest market share in 2023.
Which factors are expected to drive the product adoption?
Expansion of the 3D printing metals for personalized implants, advanced surgical tools, and biomedical innovation in healthcare will drive product adoption.
- Global
- 2023
- 2019-2022
- 210